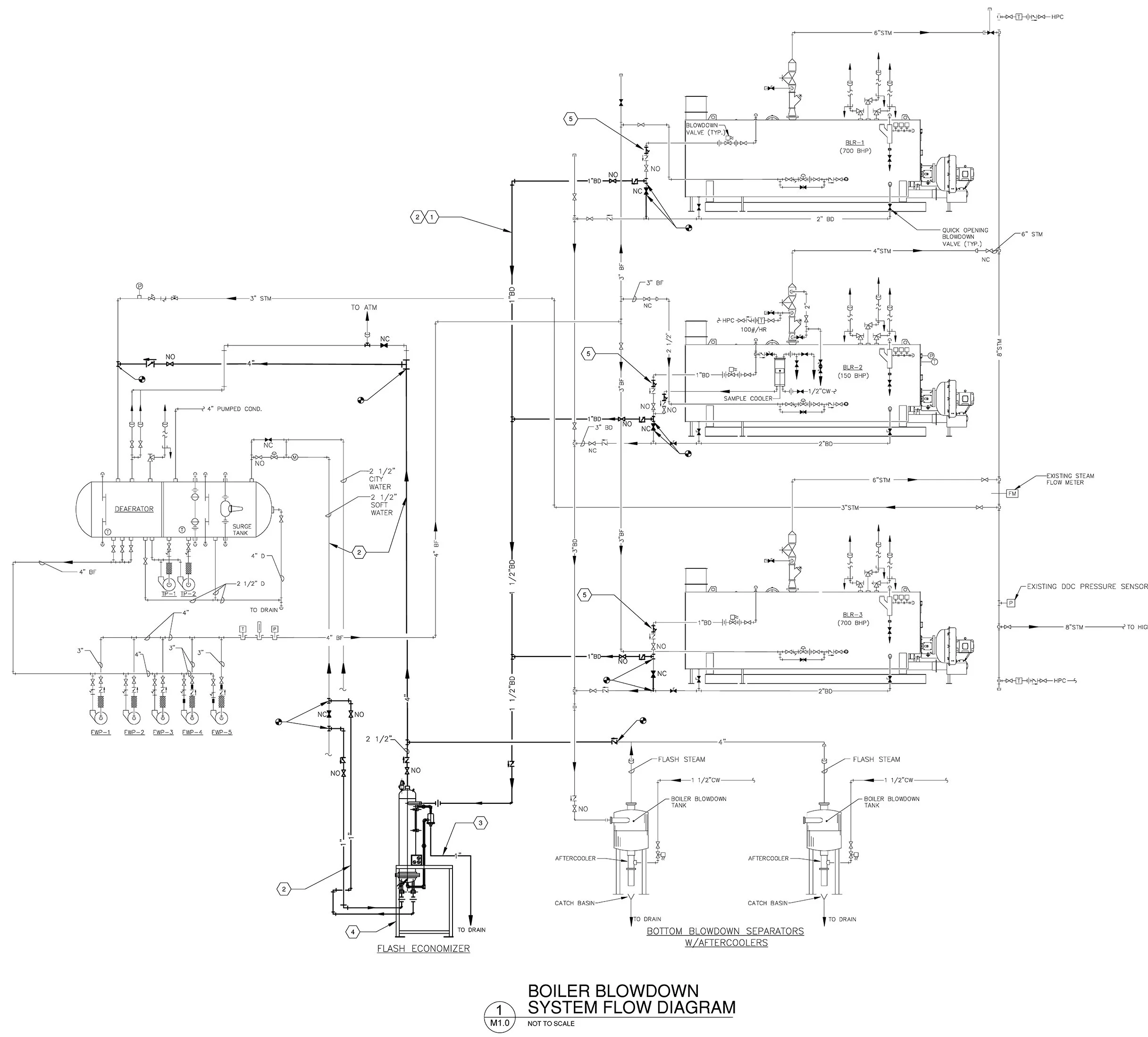
White Paper: Steam Plant Boiler Blowdown Energy and Water Savings Opportunity
PART I. GENERAL
1.01 BACKGROUND
A. This paper is meant to give a background into the potential energy and water savings methods associated steam plant blowdown recovery. While we give a broad overview of legacy and new methods of implementing such methods, the desired outcome would be for Steam Management, Inc. to work with you in a collaborative relationship to find the solutions that best fit your needs.
1.02 INTRODUCTION
A. Performance of the boiler, like efficiency and evaporation ratio reduces with time, due to poor combustion, heat transfer fouling and poor operation and maintenance. Deterioration of fuel quality and water quality also leads to poor performance of boiler. Efficiency testing helps us to find out how far the boiler efficiency drifts away from the best efficiency. Any observed abnormal deviations could therefore be investigated to pinpoint the problem area for necessary corrective action. Hence it is necessary to find out the current level of efficiency for performance evaluation, which is a pre-requisite for energy and water conservation action. The steam plant and piping distribution system safety and energy efficiency depends on the system design operation and maintenance.
1.03 WHY BLOWDOWN THE BOILER
A. As a boiler generates steam, any impurities which are in the boiler feedwater and which do not boil off with the steam will concentrate in the boiler water.
B. Boiler blowdown is water intentionally wasted from a boiler to avoid concentration of impurities during continuing evaporation of steam. The water is blown out of the boiler with some force by steam pressure within the boiler.
C. As the dissolved solids become more and more concentrated, the steam bubbles tend to become more stable, failing to burst as they reach the water surface of the boiler. There comes a point (depending on boiler pressure, size, and steam load) where a substantial part of the steam space in the boiler becomes filled with bubbles and foam is carried over into the steam main.
D. This is obviously undesirable not only because the steam is excessively wet as it leaves the boiler, but it contains boiler water with a high level of dissolved and perhaps suspended solids. These solids will contaminate control valves, heat exchangers and steam traps.
E. Whilst foaming can be caused by high levels of suspended solids, high alkalinity or contamination by oils and fats are other factors of carryover (provided these other factors are properly controlled) typically a high Total Dissolved Solids (TDS) level is the cause. Careful control of boiler water TDS level together with attention to these other factors should ensure that the risks of foaming and carryover are minimized.
F. Table 1 provides guidelines by ABMA and ASME for controlling boiler water and steam quality.
PART II. BOILER BLOWDOWN CONTROL
A. Manual Blowdown:
1. The simplest method of reducing the boiler water contamination is to take a boiler water sample, measure the TDS and if higher than recommended for the particular boiler operating criteria blowdown the water to some point well below the recommended maximum value. This is usually done once each boiler operator shift by the boiler operator. The boiler TDS gradually rises between blowdowns. A typical arrangement would be to open valve at, for example, 3,000 ppm, then close the valve at say minus 20% less or 2,400 ppm. This type of blowdown results in the highest energy and water use since it requires operating the boiler on average well below the recommended TDS level.
B. Continuous Blowdown:
1. The continuous method is an improvement to the manual blowdown where a blowdown throttling valve is used to control the TDS level. Continuous blowdown valves are special valves that have stages to reduce the problem of erosion that results in damage and subsequent failure to shut off. The continuous blow down valve position is usually set manually at a predetermined open position to maintain a maximum TDS level. This position is periodically adjusted by the boiler operating engineer based on experience and periodically sampling TDS to ensure the maximum TDS level does not get exceeded. This is an improvement over the manual blowdown but changes in the boiler output due to process or heating load swing levels are not automatically corrected.
C. Closed Loop Digitally Controlled Blowdown:
This method continuously measures the boiler water conductivity, compares it with a set point, and modulates a blowdown control valve if the TDS level is too high. Different types are available and depend on the boiler type, boiler pressure, and the quantity of water to be blown down. The benefits of the closed loop system are labor savings of automation, closer control of boiler TDS and energy and water savings.
PART III. POTENTIAL WATER AND ENERGY RECOVERY
A. Since boiler blowdown water is at a high temperature and pressure, it represents a considerable loss of energy and water.
B. The makeup water quality will determine the degree of treatment and cost associated with replacing this water in the boiler system. Table 1 provides guidelines by ABMA and ASME for controlling boiler water and steam quality. Quality ranges from unsoftened city supplied or private well systems, to softened water (which is a recommended minimal source for steam boilers, to RO or DI make up water). As the quality of the makeup water decreases, the amount of blowdown required increases to maintain the proper boiler water TDS.
C. Codes require the blowdown water to be cooled before it can be discharged to the sewer system. This is typically done by discharging the blowdown to a flash tank with the flashed steam being vented to atmosphere and the remaining condensate cooled with makeup water to below Code requirements before being discharged to drain.
D. The hot high-pressure blowdown water will flash steam when entering a low-pressure vessel for heat recovery. This low-pressure steam can be recovered and used for heating the deaerator. Deaerators are used for two main reasons, one, to remove oxygen form the boiler feedwater, and two, to help preheat the water before being sent to the boiler. The recovered flash steam from the blowdown will offset the deaerator steam consumption. The remaining hot condensate from the vessel can then be sent through a plate type heat exchanger and used to pre-heat the boiler makeup water. Thereby, saving the cooling water required to cool the condensate to below the Code requirement and the energy to pre-heat the makeup water.
PART IV. EXAMPLE
A. This example project is for a Specialty Paper Company Steam Plant with the following pre retrofit Operating Data:
1. 2 Boilers each 30,000 pounds per hours steam
2. Boiler operating pressure 150 PSIG
3. Boiler water TDS manually controlled with TDS range of (1,800 to 2,200 ppm)
4. Feedwater TDS (120 ppm)
5. Average steam rate 20,000 pounds per hour
6. Makeup water temperature 50°F
7. Deaerator pressure 30 PSIG
8. Annual operating hours 7,000
9. Fuel cost: #6 Oil $2.02/gallon, $1.33 per THERM
10. Steam plant annual fuel use 900,000 gallons
11. Boiler combustion efficiency 80.5%
12. Water cost $5.00 per 1,000 gallons
B. This example is to retrofit the steam plant with an automatically controlled closed loop digital blowdown control and blowdown heat and water recovery system. Estimated annual savings:
1. Total Annual Cost Savings: $56,000.
2. Total Annual Energy Savings: 3.12 x 109 BTU.
3. Total Annual Fuel Oil Savings: 20,700 gallons.
4. Total Annual Water Savings: 2.12x106 gallons.
5. Total Annual Carbon Dioxide Reduction: 516,260 pounds (Ref. AP-42, Vol I:1.3 Fuel Oil).
C. Click Here to View the Calculations.
If your facility is looking to complete an analysis or would like to discuss our solution based services, contact us today at:
James Moore
President & CEO
jmoore@steammgt.com